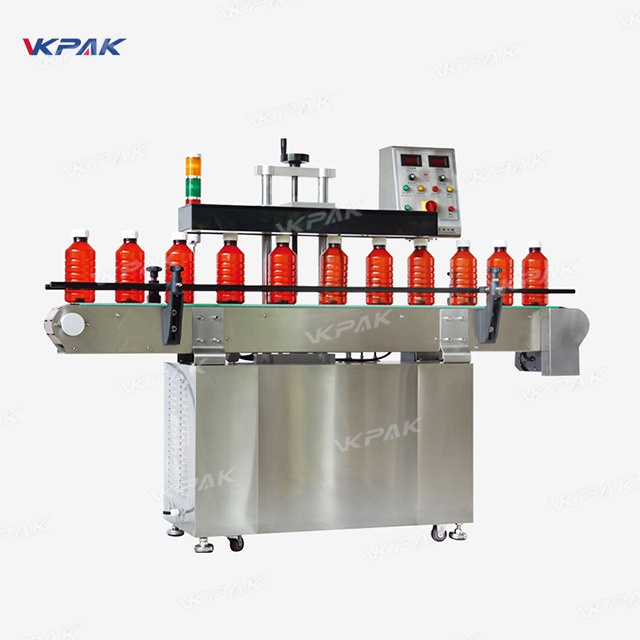
- Rated voltage: AC220V50/60Hz
- Machine Net Weight: 68kg 50kg
- The maximum power: 1800W
- Cooling Method: Cool Air / Water double cooling way
- Sealing diameter: φ15-75mm 15MM-45MM 30MM-60MM
- Bottle Height: 20-180mm
- Working methods: continue working
- Application Scope: Large Patch of Production
- Sealing speed: 0-200 bottle/min
- Packaging Dimension: 1600*450*1500mm
- Generator size: 1450*410*1300mm
The line including two main machine like induction sealing machine & inline capping machine;
The machines are suitable for capping-sealing medical bottles which is used in the analytical agent lab use. The whole line can be equipped with the auxiliary equipment like bottles turntable or the batch coding function.
As below there are basic data for the machines respectively :
Induction sealing, otherwise known as cap sealing, is a non-contact method of heating an inner seal to hermetically seal the top of plastic and glass containers. This sealing process takes place after the container has been filled and capped.
The technology of electromagnetic induction sealing with composite materials is the advanced sealing method recognized by the world now, and its characteristic of non-contact heating is suitable for sealing of plastic bottle (PP, PVC, PET, ABS, HDPE, PS and DURACON), glass bottle and various composite plastic hose, so currently it is the most advanced technology for sealing of the bottles for such industries as pharmacy, food, grease, daily chemistry, domestic chemistry, and agricultural chemistry.
Working Principle & How It Works
The closure is supplied to the bottler with an aluminum foil layer liner already inserted. Although there are various liners to choose from, a typical induction liner is multi-layered. The top layer is a paper pulp that is generally spot-glued to the cap. The next layer is wax that is used to bond a layer of aluminum foil to the pulp. The bottom layer is a polymer film laminated to the foil. After the cap or closure is applied, the container passes under an induction coil, which emits an oscillating electromagnetic field. As the container passes under the induction coil (sealing head) the conductive aluminum foil liner begins to heat due to eddy currents. The heat melts the wax, which is absorbed into the pulp backing and releases the foil from the cap. The polymer film also heats and flows onto the lip of the container. When cooled, the polymer creates a bond with the container resulting in a hermetically sealed product. Neither the container nor its contents are negatively affected; The heat generated does not harm the contents.
It is possible to overheat the foil causing damage to the seal layer and to any protective barriers. This could result in faulty seals, even weeks after the initial sealing process, so proper sizing of the induction sealing is vital to determine the exact system necessary to run a particular product.
Sealing can be done with either a hand held unit or on a conveyor system.
A more recent development (which suits a small number of applications better) allows for induction sealing to be used to apply a foil seal to a container without the need for a closure. In this case, foil is supplied pre-cut or in a reel. Where supplied in a reel, it is die cut and transferred onto the container neck. When the foil is in place, it is pressed down by the seal head, the induction cycle is activated and the seal is bonded to the container. This process is known as direct application.
Drawing
- Ammeter: Shows the current status during the operation of the whole machine.
- Working indicator: Shows the working exceptional status
- Overcurrent indicator: shows the abnormal working status.
- Power control: power controller.
- Protection reset: Recover the normal working status.
- Power switch: Controls the power of the whole machine.
- Voltmeter: Shows the voltage status during the operation of the whole machine.
- Conveyor: bottles conveying.
- Hand Wheel: adjustments for the different bottles height size.
- Lift shelves: It used to fixed and rise or fall height and low function of sealing head.
- Sealing head: Heats and seals the aluminum foil in the bottle cap.
- The speed of adjustment: the adjustment speed of conveyor belt operation button.
- Start Switch: Conveyor control switch.
- Rated voltage: AC220V50/60Hz
- Machine Net Weight: 68kg 50kg
- The maximum power: 1800W
- Cooling Method: Cool Air / Water double cooling way
- Sealing diameter: φ15-75mm 15MM-45MM 30MM-60MM
- Bottle Height: 20-180mm
- Working methods: continue working
- Application Scope: Large Patch of Production
- Sealing speed: 0-200 bottle/min
- Packaging Dimension: 1600*450*1500mm
- Generator size: 1450*410*1300mm
Use Method On Induction Sealing Machine
- Bottles height size adjustment: Put the bottle under the "sealing head", adjust the "hand wheel", make sure the distance between the "sealing head" bottom and the bottle cover face at about 1-3mm, turn the "start switch" to "on" so that the conveyor belt starts running and let the bottles go across the belt to check whether they touch the sealing head. The smallest distance without tough is the best.
- Adjust the speed of the conveyor belt with the "speed control". The aluminum foil sealing is related to the belt speed and the power. Put some bottles on the belt, turn on the "power switch" and make the sealing test. The operation formally begins once bottles are sealed firmly.
- Wait for the soft startup upon boot-strap and start the sealing 30 seconds later when the after the ammeter shows 3.2A.
- Turn off "power switch" and "startup switch" in machine shutdown.
Inline Capping Machine:
- Production capacity: 40-60 Caps /min
- Cap size: 10-50/35-140mm
- Bottle diameter: 35-140mm
- Bottle height: 38~300mm
- Size(L×W×H): 1000×800×1200mm
- Weight: 350kg
Drawing Of Inline Capping Machine
1 | Bottles | 2 | Bottles fixing |
3 | Handle for adjust position | 4 | Friction Pulley |
5 | Stroke position module | 6 | Caps pressing Cylinder |
7 | Handle for positional | 8 | Capping adjusting module |
9 | Capping cylinder | 10 | Capping Motor |
11 | Controlling box | 12 | Hand wheel |
Capping Adjustment From A To Z
Bottles Fixing Adjustment
1. Loose the handle (3)
2. Put the pre-fixed bottles (1)
3. Eyeball if the caps center is coincident with cylinder (9) center; once coincided fix the handle (3)
Capping Height Adjustment﹒
1. Loose the handle (7)
2. Adjust the handle (12) to make the capping friction wheel (4) bottom distance at 2mm to the caps bottom,fix the handle (7)
Capping Friction Gaps Adjustment:
1. Close the air source
2. Put the fixes caps between the friction wheels (4)
3. Approach the caps by moving the friction wheel (4) to adjust the stroke module (5) screw (both sides should be symmetrical by eyeballing measurement). The right fas should be 2mm to 3mm for each side;
Capping Cylinder Height Adjustment (According To Caps Samples)
1. Loose the screw (8) make the capping cylinder (9) protrude;
2. Leave the distance at 1mm-2mm from the capping nut to the tops of caps
3. Tighten the screw (8)
Capping Cylinder Speed Adjustment
1. Connect the supply power and air source to adjust the pressure setting for air pressure (standard 0.74mpa-0.6Mpa)
2. Adjust the capping time and capping interval (standard 1s to 1.5s) select the state as Manual ,Point the pedal switch to adjust the left-right friction wheel pneumatic speed ,finally it should make the speed at both speed at an equal level;
3. Adjust the capping cylinder speed.
Testing Run Of Machine
1. Take out one product for the testing run of capping; Refurbish the capper according to the capping effect;
2. Adjust the torque according to the torsion force.
Bottles Samples For Capping Sealing