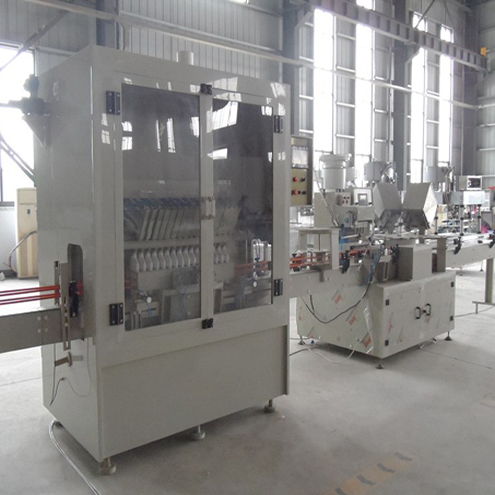
- Model: VK-FF-10 (in PP material)-10 filling nozzles
- Filling Range: 5ml-8000ml (can be set through PLC)
- Filling Accuracy: ±1%
- Working Air Pressure: 6-7kg/c㎡
- Operation Voltage: 220V/380V(available to be customized)
- Machine Weight: 1350 kg
- Machine Size: 1750x850x1900mmmm
VK-FF-10 automatic gravity liquid filling capping machine is the 3rd version of our anti-corrosive filling made specially customized according to customer's irregular-shaped bottles with angle or bent neck. It is made wholly in anti-corrosion PP standard. It is a high-tech filling equipment which is a combination of microcomputer (PLC) controlled photoelectric sensor and pneumatic actuator.
It is specially used for high corrosive such as disinfection liquid, toilet clean fluid, and so on. With features, anti-corrosive, precise filling volume, no drip, photoelectric detection, no filling when without bottle, it is the most advanced filling machine for corrosive liquid filling in china mainland.
(1) Whole machine outside frame making material uses PP material, inner structure is made of PP material, Filling nozzles are made of strong PP and high quality Alloy. More stronger than PVC and stainless steel.
(2) Filling nozzles in 3rd version, made of PP and Alloy, more stronger and longer life, in function of "Snuffback" and "eliminate bubbles", no drop and no leak.
(3) There is a overflow sensor in liquid tank, will automatically let overflow liquid into the source, not drop in machine and ground. more clean.
Customized filling nozzles system for curved-neck bottles
Specifications:
Model: VK-FF-10 (in PP material)-10 filling nozzles
Filling Range: 5ml-8000ml (can be set through PLC)
Filling Accuracy: ±1%
Working Air Pressure: 6-7kg/c㎡
Operation Voltage: 220V/380V(available to be customized)
Machine Weight: 1350 kg
Machine Size: 1750x850x1900mmmm
Cap Inserting And Capping Machine
The caps inserting feeding capping machine for irregular-shaped bottles is made of PP materials for the holding turning system
This automatic capping machine is one of our R&D products. We add a new function on it, which can automatically install the inner cap, not only can cap for out capping.
This machine is a high-tech inner cap and cap screwing machine which is a combination of PLC controlled, photoelectric sensor, servo drive and pneumatic component.
Automatic inner cap and cap screwing machine is specific to high corrosive liquid, can automatically install inner cap and screw cap for complicated-shape bottle in bleaching liquid, disinfectant, toilet cleaner, insecticide and the corrosive liquid. And designed with automatic arranging inner caps, automatic inner-cap falling, sucking, installing, automatic caps arranging, falling, screwing. Greatly reduce the manual operation.
Characters:
Made of PP material, anti-corrosive.
New and Creation function: Automatically install the inner mouth of cap.
Automatically feed the cap and capping.
PLC control.
Technical Parameters of customized capping machine for oblique bottles:
Capping Speed | Max 60 bottles / minute |
Cap Screwing Precision | 99 % |
Working Air Preasure | 6-7 kg / cm² |
Working Voltage | 220 V |
Weight | 350 kg |
Overall Size | 2000*900*1100 mm |
Filling-capping samples for special-shaped bottles:
Our Services on oblique bottles filling capping machine:
1. Installation & adjustment
After the equipment are arrived at the customer’s site, the customer is responsible for unpacking and arranging the equipment according to the placement drawing; and does under our install-adjust technicians’ guidance. Costs of the staff are decided at last.
2. Training
We are responsible for offering the technical training to user. The training content includes the structure and maintenance of the equipment, control and operation of the equipment. Through training, users' technical staff can grasp and the skill of operation and maintenance proficiently, and deal with the general troubles in time. We will appoint qualified technical staff for the guidance.
3. Quality assurance
We guarantee the line achieve product technical performance indicators within 5 days after feeding operation through the correct guidance of the installation and commissioning.
We are responsible for the fault and damage of the production line caused by our design, technology, manufacture, installation, adjustment and material defect etc. that all belong to our responsibility.
The warranty period is 12 months after acceptance check of the production line. If there is any different between the furnished equipment in the customer’s factory and the equipment concerned in the contract, the users have the right to pass the inspection book to the legal department to claim for compensation to our company within goods warranty period.
4. Warranty
Offer 12 months maintenance period to the problem that caused by our design, manufacture and the material quality, and offer the relevant parts and effective service for free for above reason. We will offer a widely and favorable technical support, after service all the time after guarantee period.