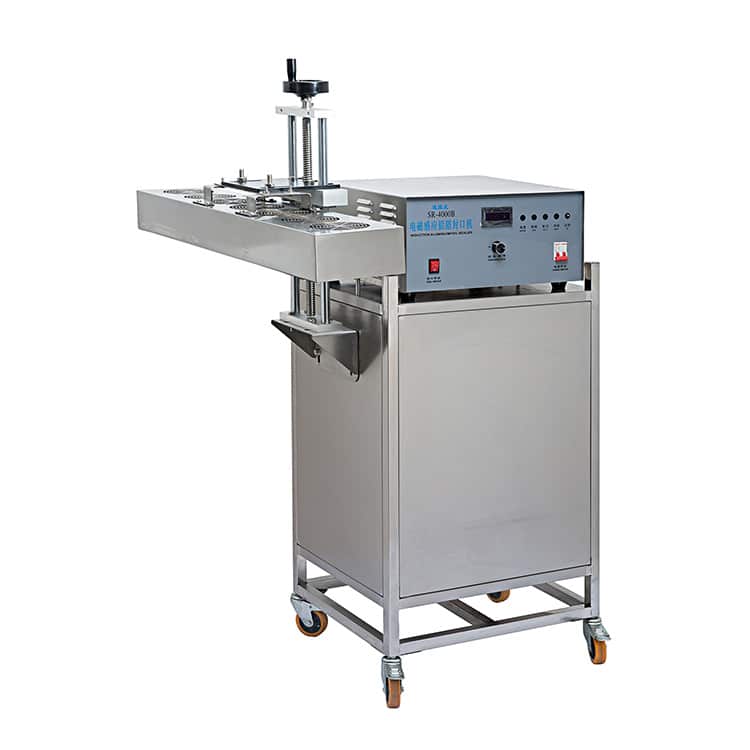
- Power: Ac 220v 50/60hz
- Sealing Voltage: 1300w
- Sealing Diameter: 15-65mm
- Machine Size: 790*320*840(Mm)
- Machine Weight: 30kg
- Chilling Mode: Air
- Operate Mode: Consistent Sealing
- Conveyor Speed: 0-12.5m/Min
Application
Mainly used in pharmaceutical, food & beverage, pesticide and cosmetic industries for a wide range of bottle sealing
Features & Characteristics
- Automatic aluminum foil sealing machine for bottles
- Good sealing performance and automatic,hot sales model
- Cheap price can be offered
- This model automatic sealing machine is easy to operate,easy to clean and move
- Our automatic sealing machine is one year warranty after you get the machine at your factory.
Basic Parameters
- Power: Ac 220v 50/60hz
- Sealing Voltage: 1300w
- Sealing Diameter: 15-65mm
- Machine Size: 790*320*840(Mm)
- Machine Weight: 30kg
- Chilling Mode: Air
- Operate Mode: Consistent Sealing
- Conveyor Speed: 0-12.5m/Min
- Sealing Theory: Electromagnetic induction seal
What Is The Induction Sealer:
Induction sealing is the process of bonding thermoplastic materials by induction heating. This involves controlled heating an electrically conducting object (usually aluminum foil) by electromagnetic induction, through heat generated in the object by eddy currents.
Induction sealing is used in many types of manufacturing. In packaging it is used for package fabrication such as forming tubes from flexible materials, attaching plastic closures to package forms, etc. Probably the most common use of induction sealing is cap sealing, a non-contact method of heating an inner seal to hermetically seal the top of plastic and glass containers. This sealing process takes place after the container has been filled and capped
The closure is supplied to the bottler with an aluminum foil layer liner already inserted. Although there are various liners to choose from, a typical induction liner is multi-layered. The top layer is a paper pulp that is generally spot-glued to the cap. The next layer is wax that is used to bond a layer of aluminum foil to the pulp. The bottom layer is a polymer film laminated to the foil. After the cap or closure is applied, the container passes under an induction coil, which emits an oscillating electromagnetic field. As the container passes under the induction coil (sealing head) the conductive aluminum foil liner begins to heat due to eddy currents. The heat melts the wax, which is absorbed into the pulp backing and releases the foil from the cap. The polymer film also heats and flows onto the lip of the container. When cooled, the polymer creates a bond with the container resulting in a hermetically sealed product. Neither the container nor its contents are negatively affected, and the heat generated does not harm the contents.
It is possible to overheat the foil causing damage to the seal layer and to any protective barriers. This could result in faulty seals, even weeks after the initial sealing process, so proper sizing of the induction sealing is vital to determine the exact system necessary to run a particular product.
Sealing can be done with either a hand held unit or on a conveyor system.
A more recent development (which suits a small number of applications better) allows for induction sealing to be used to apply a foil seal to a container without the need for a closure. In this case, foil is supplied pre-cut or in a reel. Where supplied in a reel, it is die cut and transferred onto the container neck. When the foil is in place, it is pressed down by the seal head, the induction cycle is activated and the seal is bonded to the container. This process is known as direct application or sometimes "capless" induction sealing.