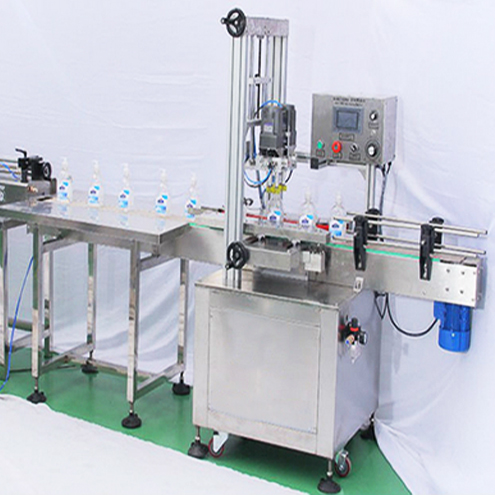
- Production capacity: 40-60 Caps /min
- Cap size: 10-50/35-140mm
- Bottle diameter: 35-140mm
- Bottle height: 38~300mm
- Size(L×W×H): 1000×800×1200mm
- Weight: 100kg
Basic Parameters
Type | VK-FC |
Production capacity | 40-60 Caps /min |
Cap size | 10-50/35-140mm |
Bottle diameter | 35-140mm |
Bottle height | 38~300mm |
Size(L×W×H) | 1000×800×1200mm |
Weight | 100kg |
Features:
Automatic screw cap machine with manual caps feeding is the latest improvement of a new type of capping machine. Aircraft elegant appearance, smart,
capping speed, high pass rate, applied to food, pharmaceutical, cosmetic, pesticides, cosmetics and other industries of different-shaped screw-cap bottle.
Four speed motors are used for cover, bottle clip, transmit, capping, machine high degree of automation, stability, easy to adjust, or replace the bottle cap when not spare parts, just make adjustments to complete.
- This screw capping machinery Suitable for automatic capping in cosmetic, medicine and drink, etc.
- Good looking,easy to operate.
- Competitive price offer.
caps for screw capping machine
bottles with caps for inline screw capping machine
Quotation: FOB (Shanghai) the below mentioned quotation based
Package: Each machine wrapped by PO film, then packed to standard wooden case.
Production Lead: 20 workdays after getting the down payment 30%, the other 70% payment collected before shipping
Guarantee: For all the machine, it claims 1 years for guarantee. (Excluded from the warranty are problems due to accidents, misuse, misapplication, storage damage, negligence, or modification to the equipment or its components. Also the easy broken spare part is not included in the guarantee)
Installation: After the machine arrive your factory, if you need, our technician will go to your place to install and test the machine and also training your worker to operating the machine (the time of train depend on you worker). The expenses (air ticket, food, hotel, the travelling fee on your country) should be on your account and you need paid for the technician usd150 per day. Also you can go to our factory to do training.
After Service: If you get the problem on the machine, our technician will go to your place to fixed the machine as soon as possible. The cost should be in your account (as above).
What Is The Capping Machine(Tightening Machine)?
Cap tightening machines are a crucial production stage for many industries, ensuring that products reach customers without leakage or spoiling. Although capping machines follow the same general principle of twisting caps onto containers, the increasing complexity of modern product designs makes finding the best machine difficult. To help you navigate the alternatives, this guide describes how cap-tightening machines work and explains the main advantages and disadvantages of each type.
Bottles and containers pass into the capping machine, which use a number of different methods to tighten caps. Each of these techniques brings its own advantages and disadvantages that depend on the container, the type and size of cap, and whether the machine works with a single product line or needs to adapt to multiple products.
Inline Screw Capping Machines
Inline screw capping machines, also known as spindle cappers, are particularly common because it is relatively easy to adjust the machines to cope with different cap types and sizes. The machines use three or four tightening discs to spin the cap as the container passes down the conveyor, and side belts grip the bottle tightly to stop it rotating and maintain a stable, upright position.
Inline machines are relatively simple to set up and the operator can manually adjust the torque and also belt, gripper, and cap feed speed. However, although the final set of tightening discs includes a clutch, it is difficult to maintain consistent torque. Accordingly, cap tightness may vary, risking an over-tight cap that proves difficult for consumers to unscrew, or a loose cap that can cause product leakage and spoilage.
Inline machines can cope with a range of cap types, including sports caps, pump caps, and trigger caps, although they may need a specialised cap feeder or a human operator to place the caps on the container ready for tightening.
Another major advantage of inline feeders is the ability to mount them over an existing conveyor section, making it easy to integrate them into a production line.
What You Should Know About Torque (Application Torque):
Variations are often introduced by inline and chuck capping equipment as well. Changes in magnetic / electrical or pneumatic settings on chuck capper heads and the speed / pressure applied by the inline spindle / belt type capping stations can influence the application and removal torque.
In a production environment the application torque is typically unknown but the capper chucks or spindle system is adjusted according to the release torque results. Generally, the higher the application torque, the higher the thread break torque. This is true up to the strip torque when the threads break / deform irreversibly during the cap tightening cycle.
If the manufacturer of the cap / bottle does not provide recommended torque specifications, it is best to start with an application torque setting that equals the cap diameter in mm divided by two (in lbfin). The release torque /applied torque quotient depends on the specific cap / bottle / liner design and the control of the previously listed variables. It is usually in the range of 0.6–0.9, higher for glass and lower for plastic bottles.
It is not uncommon to see values out of this range, but extremely high quotients typically indicate the presence of torque errors introduced in the torque measurement. As demand is continuously placed on all products to have extended shelf life, improved ergonomics, lower costs and improved appearance, application issues continue to emerge. In order to achieve maximum shelf life, the closure must create the best possible seal and the only way to ensure this is through continuous release torque monitoring at the production line.
A number of different variables can create a parasitic torque between the threads, changing the torque results or desensitising the automated release torque measurement of threaded closures. To overcome these issues it is essential to understand all the variables affecting the torque between threaded closures, optimise change parts and the configuration of the torque testing equipment accordingly.