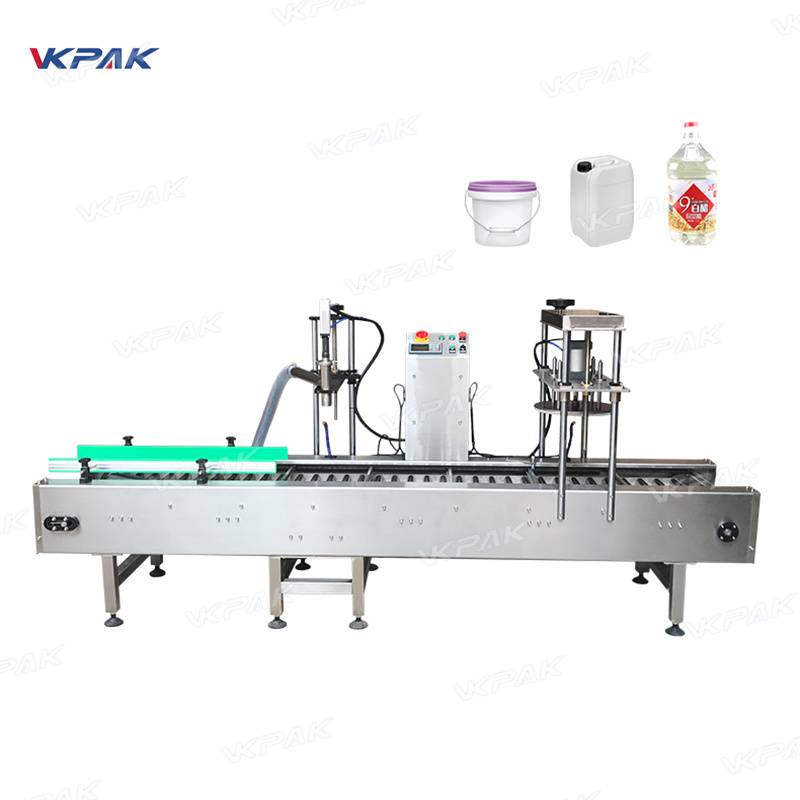
- Model: VK-WF
- Metering of filling: weight
- Nozzle quantity: 1 or 2 heads
- Accuracy: ±0.2%
- Weighing Range: 5-30kg
- Filling Speed: 120-150pcs/hour
- Air Supply: 165L/min (5.8CFM)
- Power Supply: 110V 60HZ single phase(or customized as requested)
- Dimension(mm): 1000x650x1450
- Weight: 180kg
The filling press capping machine includes mainly two machines: One is weigh filler equipment; the other bucket lids press capping machine with automatic caps feeding system.
Workflow
Working process: Put pails manually -> Conveying automatically -> Locating & Filling automatically -> Put Lids automatically -> Lids Pressing automatically -> conveying automatically.
Application Of Bucket Filling Capping Machine:
The automatic filling line is suitable for coating, paint, ink, adhesive liquid, hardener, resins, dyes, washing liquid, glycerine, lubricant oil, edible oil, flavors, solvents, additives, pesticide, daily chemicals, diluter liquid and a variety flowing liquid etc.
Features
- Filling Method: Filling from top.
- Control Mode: Manual setting filling way, micro switch control.
- Conveying Mode: Roller Type Conveying without motor
- Own digital displaying filling quantity function, can finish multi-kinds filling quantity setting.
- Automatic peeled, based on net weight filling function.
- Own vacuum withdrawing function to avoid anti-drip.
- With manual & automatic micro switch control system function.
- Dual speed control function to prevent splashing.
- With emergent treatment to avoid misuse and protect power-off.
- With SUS316 material of inside pipeline, which is liquid contact part.
- Weighing filling machine is made based on international technique, with filling and electronic weigh, electronic displaying functions.
- It is suitable for medium bucket filling of various kinds of viscous, non-viscous, corrosive and non-corrosive liquid.
Basic Parameter
- Model: VK-WF
- Metering of filling: weight
- Nozzle quantity: 1 or 2 heads
- Accuracy: ±0.2%
- Weighing Range: 5-30kg
- Filling Speed: 120-150pcs/hour
- Air Supply: 165L/min (5.8CFM)
- Power Supply: 110V 60HZ single phase(or customized as requested)
- Dimension(mm): 1000x650x1450
- Weight: 180kg
Basic Parameter Of Weighing Scale System In The Filling Machine:
Basic parameters | |
Display window | 128*64LCD/OLED English character display |
Scale interval | 1、2、5、10 |
Number of scale interval | 10000 |
Decimal place | 0、0.0、0.00、0.000 |
Unit of weight | g, kg, t(gram, kilogram and ton) |
Overall dimensions | 159(W)x 167(D)x 81(H)mm |
Product weight | About 1.2 kg |
Performance index | |
Static accuracy class | OIML R76 Class III |
Maximum signal input range | -3.6mV/V ~ 3.6 mV/V |
Maximum sensitivity | 1.5μV/d (the weakest filter) or 0.75μV/d (the strongest filter) |
Input-end noise | ≤0.5μVp-p (the weakest filter) or 0.25μVp-p (the strongest filter) |
Zero drift | ≤0.05μV(@ 0.02mV/V) |
Temperature coefficient | ≤10ppm/°C |
Input impedance at load cell interface | ≥20MΩ |
Non-linear error | ≤0.002%FS |
A/D conversion rate | 100 SPS(samples per second) |
Plastic Pail Press Capping Machine
The lid hopper products are mainly used for open barrels, paint bucket, lubricating oil drums, drums, paint bucket, hand barrels (convenience barrels) Series: 4 liters, 5 liters, 10 liters, 12 liters, 18 liters, 20 liters Standard barrel cover essential tools. Widely used in barrels, cans, lubricants, coatings, chemicals, petroleum, grain and oil, and other liquid packaging industry essential supplies.
The capping machine is an important part of the production line, is to complete the capping of the heavy bucket, the capping machine is double gland to ensure that the gland is tight and the lid is closed after the gland. The capping machine is positioned under the gland plate. After positioning, the gland is gated and the gland is pressed and pressed.
- Name: Automatic press capping machine
- Weight: 160KG
- Standard size of capping head: ¢ 34mm (can be customized)
- Capping range: 4-20L
- Dimensions: 1000 (L) x 520 (W) x 1300 (H) (mm)
- Control System: Electronic - pneumatic control
- Material: Carbon steel spray frame, no motor roller conveyor
- Capping speed: (20L barrels) 120-150 barrels / hour; (4-10L barrels) 150-200 barrels / hour
Optional Part For Transferring Materials From Storage Tank To Filling Station According To Materials Viscosity:
Bucket Samples
How To Run The Filling Capping Machine:
Unpacking
When unpacking the case, properly keep the packing list, qualification certificate, specification, and accessories and spare parts.
Installation Instruction
- The instrument should be securely mounted on the control panel of electric cabinet.
- Installation place should be free from vibration source, taking sun-proof, high temperature prevention, freeze prevention, moisture proof and rain proof measures.
Wiring Precautions
- Each ground terminal should be well grounded, correctly connected and securely fixed.
- The instrument should not share any distribution box, power socket and power lines (including ground lead) with interfering electric equipments as it would affect the performance of the instrument. If it is necessary, power filter should be added in the power circuit for isolation.
- To prevent unnecessary interference, shorten length of sensor cables as much as possible and keep sensor away from power lines and control lines.
Precautions for Use
- To prevent negative phenomena such as over high and low voltage and waveform distortion, maintain power supply stability as much as possible.
- To prevent instrument damage, NEVER press randomly, heavily and strike on instrument keypad or buttons.
- To prevent personal injury or equipment damage, NEVER dismantle the instrument at will, whether in a power-on state or not.
- The instrument allows for break-point memory and generally, after completing preset batch numbers, set manual/automatic switch under manual state before for next round of batching and then power off switch. See relevant sections for shutdown of break-point memory function.
Maintenance Precautions
- Never plug in or out the connectors on rear board or replace fuses and sensors in a power-on state.
- To prevent misalignment or imbalance, instrument calibration or setting shall only be carried out by our company personnel or professional.
- Do not clean instrument with organic solvents of HC, alcohol and ketone type, or with strong acid or alkali solution as it would damage instrument enclosure, panel and internal components.
- No arbitrary repair or modification to the instrument is acceptable and, in case of equipment failure, please follow the operating instruction or contact with us, or otherwise no preferential after-sales service would be offered.
- The equipment, if left unused, should be powered on at least once every month with a period of more than 1h, removing internal moisture.