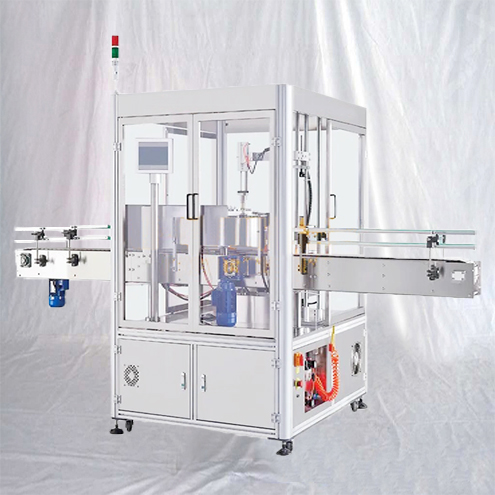
- Model: VK-HMGL-S
- Power: Three-phase 380V 50 Hz 3000W
- Length: 3650mm
- Equipment width: 1450mm
- Conveyor line speed: 20m/min (conveyor line speed can be adjusted according to actual production conditions)
- Speed adjustment method: Sectional speed adjustment
- Max label dispensing speed: 60 m/min Maximum labeling speed: 20 pcs/min
- Labeling accuracy: ±1mm (requires customer bottle size error within ±0.3mm)
- Product size: square bottle
- Maximum label width: 160mm
- Maximum label length: 600mm
- Maximum label diameter: 600 mm Paper core diameter:152mm
- Whole machine weight: about 1200 Kg
This is a new continuous hot melt adhesive OPP labeling machine. It can automatically adjust the in and out transmission of the container; The containers which are separated by the bottle separation screw and kept in a distance according to the spacing of the star wheel are transferred to the container turntable. After the container is fixed by the bottle pressing mechanism and the mold seat of the container, the container starts to rotate at a certain speed, and the bottle is mechanically pre-positioned during the rotation of the product. The label is labeled in a specified position.
Operation Process Of Hot Melt Glue Labeller Equipment:
When the container reaches the detection position of the electric eye, the computer controls the label delivering system to deliver the label. When a label delivering action is completed, the high-speed cutter cuts a label. The labeling accuracy and stability is ensured with the help of Sanyo small inertia high-speed servo motor.
The cut labels are sent to the gluing system which applies glue to both the leading and trailing edges of a label. This gluing method consumes the least consumption of hot melt adhesive.
When the glued label is transferred to the labeling position, the label can be accurately and effectively adhered to the container. Since the container is in a rotating state during the transfer process, the label can be affixed to the container smoothly and tightly. The adhesive strip at the end of the sizing can form a good label lap seal, completing a labeling process.
Main Part
A: Host
- Sanyo Servo System
- Sanyo Servo Drive System
- FLEXEM 7-inch HMI
- Pansonic high-resolution color label sensor
- Pansonic high-resolution gluing and missing detection sensor
- Pansonic product detection sensor switch
- Pansonic pressure sensor
B: Mechanical Part
- Conveying mechanism: 90W Taiwan Chenggang Motor
- Conveyor belt: Industrial film-based conveyor belt
- Main motor: 1500W Italian BOEM AC motor (with original BOEM reducer)
- Bottle separation mechanism: Rodless cylinder bottle separation mechanism
- Positioning mechanism: Stepper motor positioning and labeling
- Labeling mechanism: The stepper motor drives the bottle and performs labeling during rotation
- Label delivering mechanism: Yujun servo film delivering system (high-speed servo motor drive)
- Pressing mechanism: brush assembly
- Bottle guide mechanism: Profile guide rail with dual coordinate adjustment
- Glue supply system: Yujun specialized hot melt glue supply system (German Siemens control system) to ensure the accuracy and uniformity of glue application
Hot Melt Labels Applicator Equipment Safety Protection:
- Safety protection: close the protection door.
- Label shortage alarm: Set the alarm when the label is running out to remind the operator to replace the label
- Bottle shortage alarm: when there is a shortage of bottles, the equipment will stop and alarm; when there are bottles, it will automatically resume production, which is convenient for on-line production
Labeling Missing Alarm
- Air pressure detection: When the air pressure does not meet the production requirements, the equipment will shut down automatically.
- Vacuum detection: When the vacuum does not meet the production requirements, the equipment will shut down automatically.
- Temperature detection: When the temperature of the hot melt adhesive does not meet the production requirements, the equipment will shut down automatically.
Technical Parameter
- Model: VK-HMGL-S
- Power: Three-phase 380V 50 Hz 3000W
- Length: 3650mm
- Equipment width: 1450mm
- Conveyor line speed: 20m/min (conveyor line speed can be adjusted according to actual production conditions)
- Speed adjustment method: Sectional speed adjustment
- Max label dispensing speed: 60 m/min Maximum labeling speed: 20 pcs/min
- Labeling accuracy: ±1mm (requires customer bottle size error within ±0.3mm)
- Product size: square bottle
- Maximum label width: 160mm
- Maximum label length: 600mm
- Maximum label diameter: 600 mm Paper core diameter:152mm
- Whole machine weight: about 1200 Kg
Remark:
- Power: 14Kw
- Gas consumption: 6Kg, 8L/min;
- Power supply voltage: three-phase 380V
- Production capacity: 1200 bottles/hour
Details
The following table is a detailed list of the main electrical components of each hot melt adhesive labeling equipment.
Serial No. | Item Name | Brand | Country | QTY | Remark |
1 | Label delivering servo motor | Sanyo | Japan | 1 | 750w |
2 | Label delivering servo driver | Sanyo | Japan | 1 | 750w |
3 | Frequency converter | Danfoss | DenMark | 3 | |
4 | Air switch | Merlin | France | 1 | |
5 | Circuit Breaker | TE | France | 1 | |
6 | Relay | Omron | Germany | 3 | 24V |
7 | Emergency stop switch(one at the front and one at the rear) | TE | France | 2 | |
8 | Switching power supply | MeanWell | TaiWan | 1 | 13A |
9 | Control cable | China | Multi-core shielded wire | ||
10 | PLC | Siemens | Germany | 3 | |
11 | HMI | FLexem | China | 1 | |
12 | Detection sensor | Panasonic | Japan | 3 | |
13 | Label detection sensor | Panasonic | Japan | 1 | Digital display adjustment |
14 | Main power motor 1500W | BOEM | Italy | 1 | Inverter speed regulation |
15 | Main power motor reducer | BOEM | Italy | 1 | |
16 | Conveyor belt motor 90W | Chenggang | TaiWan | 1 | Inverter speed regulation |
17 | Conveyor belt motor reducer | Chenggang | TaiWan | 1 | |
18 | Gluing motor 1:20 | Panasonic | Japan | 1 | |
19 | Acoustic speed control Motor 60W | Panasonic | Japan | 1 | |
20 | Stainless steel Material | China | |||
21 | Conveyor belt chain plate | Industrial Type |
What Is The Hot Melt Adhesive?
Hot melt adhesive (HMA), also known as hot glue, is a form of thermoplastic adhesive that is commonly sold as solid cylindrical sticks of various diameters designed to be applied using a hot glue gun. The gun uses a continuous-duty heating element to melt the plastic glue, which the user pushes through the gun either with a mechanical trigger mechanism on the gun, or with direct finger pressure. The glue squeezed out of the heated nozzle is initially hot enough to burn and even blister skin. The glue is sticky when hot, and solidifies in a few seconds to one minute. Hot melt adhesives can also be applied by dipping or spraying, and are popular with hobbyists and crafters both for affixing and as an inexpensive alternative to resin casting.
In industrial use, hot melt adhesives provide several advantages over solvent-based adhesives. Volatile organic compounds are reduced or eliminated, and the drying or curing step is eliminated. Hot melt adhesives have long shelf life and usually can be disposed of without special precautions. Some of the disadvantages involve thermal load of the substrate, limiting use to substrates not sensitive to higher temperatures, and loss of bond strength at higher temperatures, up to complete melting of the adhesive. This can be reduced by using a reactive adhesive that after solidifying undergoes further curing e.g., by moisture (e.g., reactive urethanes and silicones), or is cured by ultraviolet radiation. Some HMAs may not be resistant to chemical attacks and weathering. HMAs do not lose thickness during solidifying; solvent-based adhesives may lose up to 50–70% of layer thickness during drying.
Applications of HMA
Hot-melt adhesives are as numerous as they are versatile. In general, hot melts are applied by extruding, rolling or spraying, and the high melt viscosity makes them ideal for porous and permeable substrates. HMA are capable of bonding an array of different substrates including: rubbers, ceramics, metals, plastics, glass and wood.
Today, HMA (hot-melt adhesives) are available in a variety of different types, allowing for use in a wide range of applications across several industries. For use with hobby or craft projects such as the assembly or repair of remote control foam model aircraft, and artificial floral arrangements, hot-melt sticks and hot-melt glue guns are used in the application of the adhesive. For use in industrial processes, adhesive is supplied in larger sticks and glue guns with higher melting rates. Aside from hot melt sticks, HMA can be delivered in other formats such as granular or power hot melt blocks for bulk melt processors. Larger applications of HMA traditionally use pneumatic systems to supply adhesive.
Examples Of Industries Where HMA Is Used Includes:
- Closing the flaps of corrugated boxes and paperboard cartons in the packaging industry.
- Spine gluing in the bookbinding industry
- Profile-wrapping, product assembly and laminating applications in the woodworking industry
- Disposable diapers are constructed through the use of HMA, bonding the non-woven material to both the backsheet and the elastics.
- Many electronic device manufacturers may also use an HMA to affix parts and wires, or to secure, insulate, and protect the device's components.