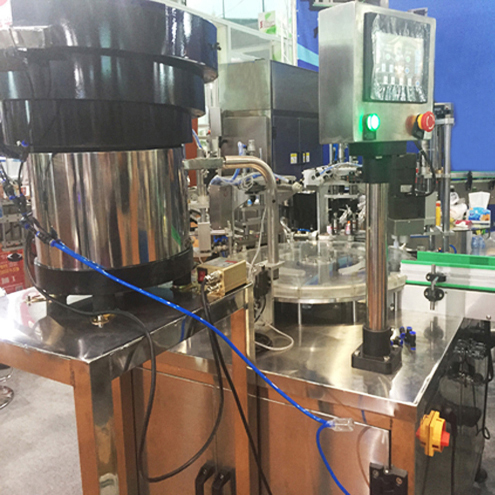
- Model: VK-MFC
- Filling Volume: 1-150ml
- Output: 30-50 Bottles/min
- Filling Precision: less than ±1%
- Power Supply: 220V/50Hz (customized according to customer’s requirements)
- Capping Rate: more than 99%
- Stoppering rate: more than 99%
- Labeling rate: more than 99%
- Air Supply: 1.3 m3/h 0.4-0.8Mpa
- Power: 2.0 kw
- Weight: 650 kg
- Dimension: 6000*3200*1750mm
Product overview for small bottles filling capping line
Suitable for the applications of 5-100ml liquid filling and sealing in pharmaceutical industry, the VK-MFC small dose liquid filling machine is with reasonable structure, high precision indexing table for filling, capping, cap pressing,precision peristaltic pump filling; The machine is controlled by the PLC with the advantage of easy operation and maintenance. There is the system for functioning as no filling without bottles feeding, no plugging without bottles sensoring, no capping without pluggers. The filling line, made of the stainless steel as its platform for working, is in line with GMP standard. The machine controlled by pneumatic and electric dual system in the machine adopts the mechanical transmission, which can transmit the power in stable and lower power-consumption plus the accurate positioning features. The filling line is especially used in the mass production.
Application of filling line :
Main Technical Parameter of filling capping labeling line :
Model: VK-MFC
Filling Volume: 1-150ml
Output: 30-50 Bottles/min
Filling Precision: less than ±1%
Power Supply: 220V/50Hz (customized according to customer's requirements)
Capping Rate: more than 99%
Stoppering rate: more than 99%
Labeling rate: more than 99%
Air Supply: 1.3 m3/h 0.4-0.8Mpa
Power: 2.0 kw
Weight: 650 kg
Dimension: 6000*3200*1750mm
Basic configuration of Filling line
Number | Item | Brand |
1 | PLC | MITSUBISHI(Japan) |
2 | Cylinder | AirTAC (Taiwan) |
3 | Peristaltic pump | China |
4 | Conveyor belt slat | China |
5 | Reducer box | Zhongda(Taiwan) |
6 | Touch screen | WEINVIEW(Taiwan) |
7 | Electromagnetic | SHAKO (Taiwan) |
8 | photoelectric | Autonics (Korea) |
9 | Sudden Stop | Schneider(French) |
10 | Contact Materials | 316LStainless |
11 | Relay | OMRON(Japan) |
12 | AC contactor | Schneider(French) |
13 | Switch | Schneider(French) |
14 | Inverter | DELTA(Taiwan) |
15 | Motor | Shanghai Maily |
Spare parts for filling monoblock
Number | Item | Quantity |
1 | Brush | 1pc |
2 | Silastical bar for feeding | 2pcs |
3 | Silastical bar for output | 2sets |
4 | Solenoid valve | 1pc |
5 | Throttle | 2pcs |
6 | Glass Valve | 2pcs |
7 | Motor Belt | 1pc |
8 | Synchronizer belt | 1pc |
9 | 82.6mm belt slat | 5sets |
10 | Open-ended spanner | 1set |
11 | Hex Wrench | 1set |
12 | Slotted screwdriver | 1set |
13 | Plus screwdriver | 1set |
14 | Spanner | 1set |
Main parts & working principle
Bottles unscrambler system
Bottles caps & inner plugger vibrator
1. The machine is constituted of such parts as conveyor belt, sketch of machine, vibrator for bottles & caps, peristaltic pump etc.
2. Prepare sufficient bottles, plugs, caps and liquid. The plugs and caps shall fill fully the vibrating tracks and at the plugging and capping work stations. The bottles are to be delivered by conveyor belt to the indexing star wheel, then the bottles will be delivered intermittently by the indexing star wheel to the filling, plugging and capping positions.
3. The liquid is to be sucked in by the peristaltic pump and then delivered by the silicone tubes. Finally the liquid will be filled into the bottles by the needle tubing which are moving automatically up and down. For each moving up and down the needle tubes, two cycles of filling is done. The filling is completed by the cyclic insertion of filling nozzles into the bottles. With no-bottle detecting photoelectric eye, if there is no bottles on the work station, the peristaltic pump stops work as no bottles can be detected.
4. The plug vibrating bowl delivers the plugs to the plug inserting station, meanwhile the filled bottles are transferred intermittently by the indexing star wheel to the position under the plugging station.
5. Then the cylinder drives the plug inserter to dive downward and push the plugs into the bottles. The plug inserted bottles will be transferred by the indexing star wheel to the cap falling and capping stations
6. The capping head spins and moves up and down as a whole. When the bottles stop under it, the downward capping head clutches the caps and finishes capping. With plug detecting photo-electric eye, once there is no bottles on station or there is bottle but no cap, then the cap pressing mechanism will stop motioning as no inner plugs can be detected. By doing this, the finished product can be avoid being without inner plugs. The capping is mainly achieved by the up and down spinning motions. The capped bottles are delivered to the end of machine and the next cycle is ready.
7. The working process of machine
Maintenance
1. It is necessary to check and maintain the machine to elongate the machine and optimize the function of machine; The working machine should be maintained every three month; The bearing and gear transmission part must be lubricated with the grease; The lubrication must be done periodically; The slide way oil (N68) should be added into the part like reciprocating mechanism motion or lifting two times every day; The automobile oil(N68) should be added into the rotary or swinging parts; Every half month add the grease into the cam slot; Every month one time for oil nozzle by adding the grease;
2. Never use metal tools to hit or scrape the surface where the bonding is conglomerated on the parts like components or mold.
3. If the machine stops running for a long time add the grease for lubrication in the parts like transmission or bearing part; Also treat the machine with water-proof protection.
4. Never put any objects on the machine lest it damage the machine.
5. Clean the dust inside the components periodically also check all the screws and fix any screw loosened.
6. Check the screws in the terminals for wiring at a certain time and be sure the screw is fixed;
7. Check if there be any loose station in the stretched wiring path from the electric boxes; If the part is too loose re-fix the screw in order to avoid the abrasion or damage in the insulation layer which may cause the electric leakage;
8. Check the easily-worn pats and change the damaged one on time;
Packaging & Transportation
Never lay the machine horizontally or upright down ; Dissemble the foot of machine and fix the whole machine with the bottom of crate. The machine should keep still in the crate without any loose from the crate or shake station during shipping;
The packing of machine should be neutral; When moving the machine please use the forklift truck or crane and move the machine from the bottom in stable movement; Notice the illustration in the picture as below; when hoisting and swinging the machine the crane should not be allowed to contact the machine. Fix the machine with 4pcs M16X200 of bolts then link the cranes and the bolts for hoisting and swinging of machines. Meanwhile to cushion the protection objects under the machine. Use the strut for stable hoisting if necessary (illustrated as below in fig)
Before unpacking the crate check if there be any damage on the crate; If any damage occurs on the crate do not open the crate and contact the shipping company immediately; Open the crate under the scrutiny from the shipping workers and record the process;
As far as the safety is concerned the distance from the ground for the forklift truck should be kept below 1m; If using the crane moving the machine the distance should be kept from 2meters to 2.5meters.