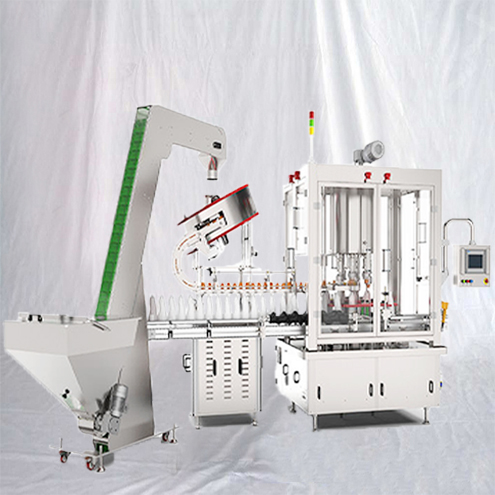
- Dimensions: 2000mm (length) * 1800mm (width) * 2800mm (height)
- Capping head: 8 heads
- Stand-alone pass rate: 99%
- Speed: 80bpm
- Voltage: 220V-380v, 50-60HZ(Based on requirements)
- Total power: 5kw
- Air source required: 0.6Mpa clean and stable air source
- Running noise (decibel): ≦80 decibels
- Machine weight: 3.5 tons
- Machine material Frame: carbon steel outsourcing stainless steel frame;
The pump caps screw capping machine high speed type is composed of several main parts, including bottle/cap feeding automatic cap elevator and unscrambler inlet and outlet bottle templates capping mechanism rejection mechanism electrical control etc.
Drawing
Features
- PLC controlled, integrated cap feeding, grasping, inserting and rotating ( can affiliate with automatic cap sorting machine to realize full automation)
- Production capacity can achieve 80bpm with 8 heads
- Gentle operation, no scratch and injury to caps and containers
- Quick changeovers
- Module structure, manipulate on the touch screen, easy maintenance
- Suitable for different sizes of caps, applicable in daily chemical industry
- Easy connected to filling machine and labeling machine
- Low running noise
Working Principle
Bottle-Feeding By Screw Rod
The bottle-in screw is processed by contour design, with precise and fast bottle feeding; Gentle movements, no damage to bottle. The screw drive follows the main drive, the screw angle can be set via touch screen to make it match with the star wheel. There is a sensor at the bottle-in screw, no bottle, no capping and alarm when bottle-stuck.
Servo Cap Feeding:
The screw capper adopts servo motor for cap-feeding chain. The servo motor has the advantages of periodic start and stop, periodic positive and negative rotation, not only reducing noise and avoid cap-stuck.
Cap-Dividing
The cap divider is customized by the cap shape and different diameters would require changeover, but only the white part in the following pic needs to be changed.
Servo Capping:
The screw capping machine uses the Siemens drive system, which combines the control system and servo motor in an ultra-compact unified system for maximum flexibility in minimal space and 90% reduction in wiring. In the process of capping, the servo motor can control the capping curve movement in sections, and at the same time can ensure smooth segmentation process, and realize the digital capping torque control, which is completely superior to the traditional clutch torque control.
- Closed loop control by the servo motor and program throughout the capping process;
- Automatically adjust the capping force until the set torque is reached;
- Due to the precise and flexible control of the motion drive module and program, the influence of the inertia of the capping head and the deviation of the parts can be eliminated;
- Torque switching between different products can be achieved simply by changing the set value of the program.
Note: For the 8-head capping machine for trigger cap, the capping heads are different:
It adopts permanent magnet clutch to control cap torque.
- During capping process, torque evenly spreads to four wheels
- Make non-relative motion between wheels and caps
- Keep static station between wheels and bottles during capping
- High-precious torque control system, a stable and reasonable torque value
Changing Different Products-Templates
Made of PP, designed by bottle shape, with smooth surface. It can not only stabilize the positioning, prevent the bottle from being scratched; and allows quick changeover.
For different specifications of products, it adopts quick-release design. The templates are color-coded to distinguish between different specifications.
Rejection System
Dual-conveyor equipped after capping. The qualified products are normally transported, and the unqualified ones (no cap, no inner tube, misapplied cap) will be automatically split to another conveyor by swing cylinder. When bottle block appears, the capping machine will automatically stop and it will start again when the problem solved.
Safety Door
All doors are installed with limit switch to make sure machine stops and sends warning signal when door is open. All production area machines with movable guard are electrically interlocked to completely shut down the main drive and control circuit and bring all machine movement to a rapid stop immediately upon opening the guard.
Main Technical Parameters
- Dimensions: 2000mm (length) * 1800mm (width) * 2800mm (height)
- Capping head: 8 heads
- Stand-alone pass rate: 99%
- Speed: 80bpm
- Voltage: 220V-380v, 50-60HZ(Based on requirements)
- Total power: 5kw
- Air source required: 0.6Mpa clean and stable air source
- Running noise (decibel): ≦80 decibels
- Machine weight: 3.5 tons
- Machine material Frame: carbon steel outsourcing stainless steel frame;
- Screw cap contacting with cap: polyurethane (PU) ;
- Screen door: stainless steel edging, plexiglass; electrical box: stainless steel;
- Connection and fixing mechanical parts: carbon steel, stainless steel, etc.;
- Seal: rubber
Major Technical Components
- PLC: Siemens
- Touch screen: Siemens
- Servo: Siemens
- Breaker: Schneider
- Frequency converter: Siemens
- Button: Schneider
- Alarm light: Schmersal
- Safety door switch: Schmersal
- Sensor: SICK/IFM/LEUZE
- Remote module: Fbox-WIFI(for instant communication and remote control)
If the above brands are out of stock, we will choose equivalent brands instead.
Automatic Cap Elevator And Unscrambler
- It is to arrange the disorderly spray cap regularly by vibrating principle and round cap by positioning plate. The cap is outputted from the cover channel in an orderly manner, and the capping machine is grasped by the distribution plate.
- The speed of the unscrambler is automatically adjusted according to the elevator. The elevator is connected with the unscrambler, and automatically controls the cap-sending speed, which is matched with the whole line speed.
- The unscrambler is automatically controlled by the capping machine interface, without manual adjustment.
- The parameters can be stored.
- Quick changeover.
The line can be integrated with the high speed filling machine to form the whole line: