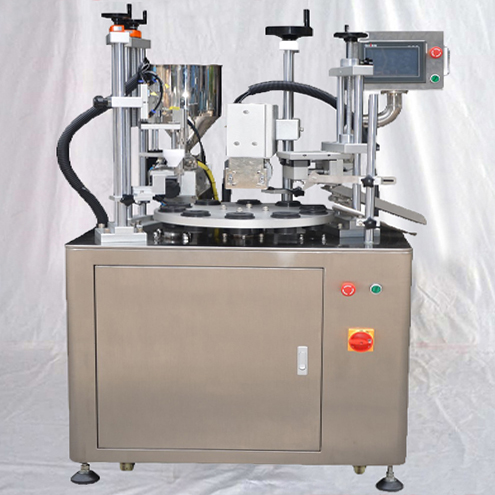
- Model: VK-TFS-006U
- Power supply: AC220V 50/60HZ singe phase
- Power: 2KW
- Filling Range: A:5-30ml B: 6-60ml C: 10-120ml D: 25-250ml E: 50-500ml
- Sealing Dia.: 5-50mm
- Max.height: 5-200mm
- Capacity: 20-30tubes/min
- Dimension: 1300*900*1550mm
- N.W: 350kgs
- HS code: 8422 303090
- Machine Body: 202# stainless steel
The ultrasonic sealing machine tubes filling equipment is linked with ultrasonic sealing, the heat required for melting is only generated inside the thermoplastic sealing layer. For localized conversion of vibrations to friction heat, the anvil or sonotrode profiles are mostly linear and include radii or small plateaus. These profiles ensure focusing of the energy input and therefore short sealing times between 100 and 200 milliseconds. With ultrasonic sealing heat is generated at the inside of the film, not by heat input from the outside as is the case with heat sealing, for example. The tools (sonotrode and anvil) that come into direct contact with the packaging material, remain cold during the entire weld process. The support layer remains almost cold and upon termination of energy input, the heat dissipates faster to the outside due to the temperature difference between the support layer and the sealing layer so that the hot-tack resistance is significantly higher.
Ultrasonic Sealing Is Particularly Well Suited For:
- Thermoplastic films (pouches and bags) Tubes, trays, and cups
- Tubes, trays, and cups
- Cardboard packaging with thermoplastic coating
- Valves and vents on films / filter materials
- Screw caps on coated cardboard packaging / films
When choosing tube filling equipment for plastic tubes, it is very important to understand the various types of tube sealing options available. Tube filling machinery comes with hot-air sealing, ultrasonic sealing, impulse sealing or hot-jaw sealing options. Matching the type of squeeze tube with the correct tube sealing equipment is very important to ensure strong, professional tube seals. Each tube material behaves differently so what works well for a mono layer polyethylene cosmetic tube, may not work so well with a multi-layer COEX tube. Depending on the industry for a given product, such as cosmetic tubes, personal care tubes, pharmaceutical tubes, or household & industrial tubes, choosing the correct tube filling & sealing equipment can be challenging. Lets take a look at the two most popular options currently used in the tube packaging industry today.
Hot Air Tube Sealers
The most popular tube sealing machinery option is hot-air tube sealing. With this system hot air is generated and blown into the open end of the plastic or laminate tube. This heated air penetrates the plastic tube wall heating the material enough to make it soft and pliable. A set of tube sealing jaws then crimps the softened plastic to weld the open end closed. The primary advantage of this tube sealing technology is it’s speed. Another advantage is hot air sealers work with the largest range of laminate or plastic tubes. Whether the tube material is LDPE, MDPE, HDPE, PP, Mono layer or multi-layer with or without EVOH barrier protection, hot air tube sealing should work. A disadvantage however is the need for specific hot air nozzles sized to each diameter tube that is filled and sealed. This will add to the cost of change parts needed for the tube run. The cost of format parts are minimal however when factored over the production run size at higher throughput. We recommend this style of tube filler if the production run sizes are greater than 20,000 tubes.
Ultrasonic Tube Sealers
Ultrasonic tube sealing is another popular option found in the packaging industry today. Standalone tube sealers using ultrasonics are popular for small volume tube runs. Tube filling machinery can also be retrofitted with ultrasonic tube sealing systems as an alternative to hot air sealing. With ultrasonic tube sealing, plastic and laminate tubes are sealed by high frequency vibration of an ultrasonic sealing horn. This high frequency vibration generates intense heat at the tube wall which causes the polyethylene tube plastic to soften. The open end of the plastic tube is held closed under pressure from the sealing horn and matching sealing anvil, thus forming a strong weld. Advantages of sealing tubes with ultrasonic technology are the ease of use, no need for custom-made size parts, and ability to seal through product contamination in the seal area such as happens when overfilling a tube with product. The disadvantage however is lower tube sealing speed compared to hot-air sealing. As far as our ultrasonic sealing machine is concerned, the basic information given as below:
- Plastic composite hose filling and sealing machine made of stainless steel, using the buttons to control the work process: artificial tubes, automatic rotary,quantitative filling, automatically cut off, heating sealing, cut tail, finished exit.
- All work using the full cylinder stroke control, easy to adjust filling volume, the filling speed can be adjusted.
- It applies to all kinds of plastics and composite hose filling, sealing, date printing, cut tail. Sealing neat appearance, sealing strong, high accuracy, good stability.
Basic Parameters
Compressed air | Pressure: 0.4-0.6MPA Consumption: 0.3M3/MIN |
Scope of work | A type :5-15ML B type :10-75ML C-type :20-150ML D-type :50-300ML E-type :100-500ML F type :200-1000ML |
Production capacity | 10-80 times / min |
Filling accuracy error | <2% |
Table adjustable height | 100MM |
Tank Capacity | 20L, 30L, 40L, 50L |
Filling the container diameter | according to the material viscosity and filling volume set |
Note: The above parameters for reference only.
The machine constantly upgrades parameters may cause the actual discrepancies, please understand.
How Ultrasonic Sealing Works
The ultrasonic tube sealer is designed to be mounted onto virtually all styles of filling machines. As the tube is advanced to the ultrasonic tube sealing station, a switch closes to initiate the weld cycle. Air is directed into cylinders to advance the weld anvil and ultrasonic horn towards the center line of the tube.
The tube is closed to a preset gap and held for the applica-tion of sonic energy.
An ultrasonic power supply takes the 50/60 Hz electrical energy and converts it to 30,000 cycles per second thorough a power oscillator.
This high frequency electrical energy is applied to the convertor which transforms the electrical current to high frequency mechanical vibrations.
The sonic energy causes the horn to vibrate against the tube end at 30,000 cycles per second.
The intense vibration disperses any contamination from the seal area and generates heat to bond the material.
The energy is then stopped and the tube is held closed for a brief time (typically .05 to .150 seconds).
Then the tube goes to the next station on the filling line. Typically cycle times range from 45 to 80 units per minute, depending on tube diameter and material.
Product Features
- The machine can be used for explosion-proof units.
- Mainly used for quantitative filling of water, oil, lotion, paste-like material. According filling needs, adjustable work surface lift.
- Filling volume 5-1000ML, Divided into six series: A, B, C, D, E, F.
- Feeding mode: Normal Gravity / automatic suction type Choose one.
- Control: pneumatic control
Workplace For Tubes Filling Sealing Machine Semi Automatic
1. Laboratory
2. Industrial production operations with continuous processing line
Detailed Pictures
Tubes Samples